The Comprehensive Guide to Injection Mold Plastics
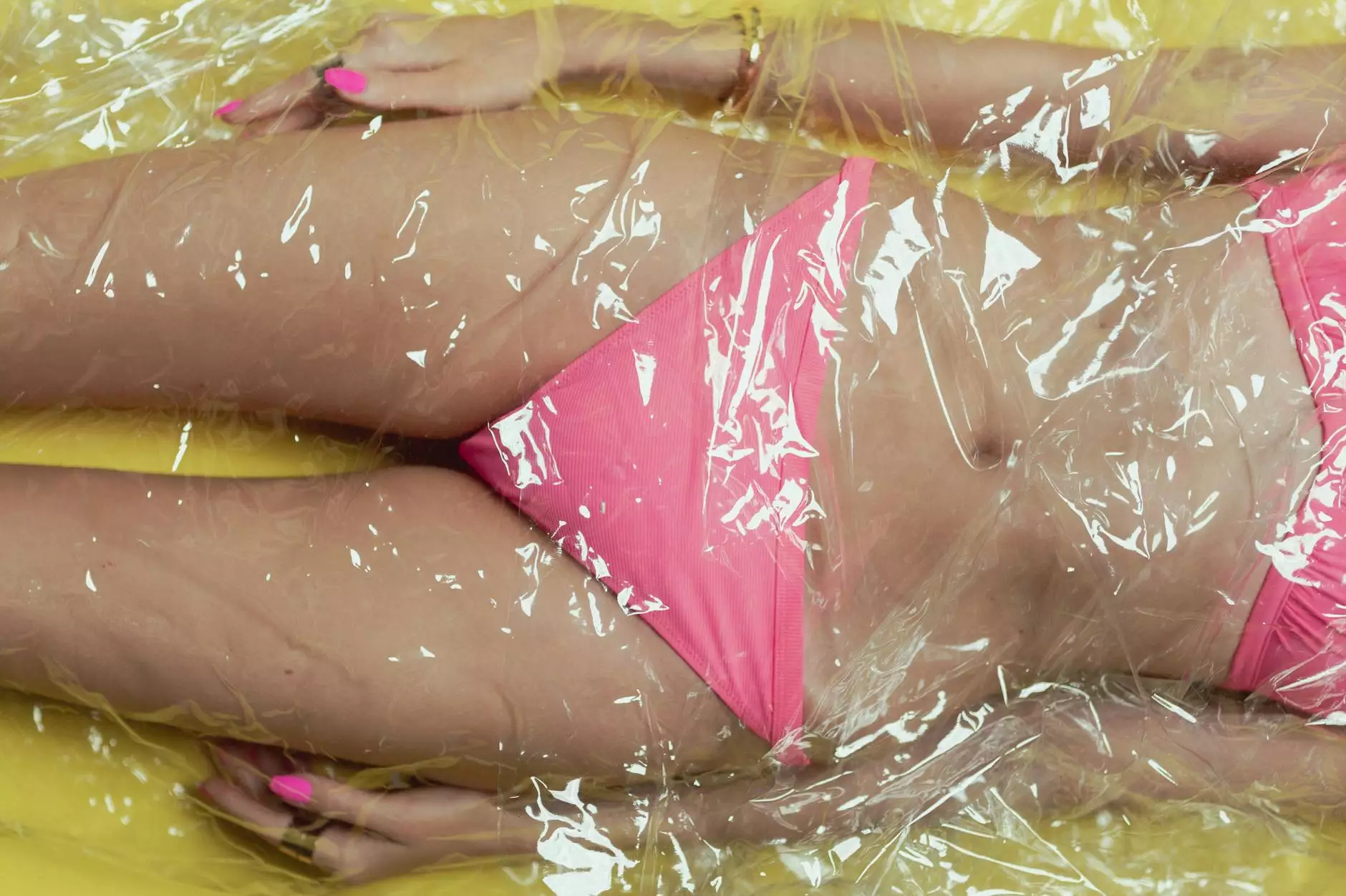
Injection mold plastics have transformed the manufacturing landscape by offering efficient, high-quality, and cost-effective solutions for producing complex plastic parts. This comprehensive guide delves into the technical aspects, benefits, applications, and future trends of injection mold plastics, illustrating their significance in various industries.
What is Injection Molding?
Injection molding is a manufacturing process for producing parts by injecting molten material into a mold. The process involves several stages:
- Material Preparation: Raw plastic material is fed into a heated barrel where it is melted.
- Injection: The molten plastic is injected into a mold cavity under high pressure.
- Cooling: The injected material cools and solidifies, taking the shape of the mold.
- Mold Opening: The mold is opened, and the finished part is ejected.
This method is highly efficient, allowing the production of intricate shapes with precision and minimal waste.
The Role of Plastics in Injection Molding
The choice of injection mold plastics significantly influences the quality and characteristics of the final product. Different types of plastics are utilized based on their mechanical properties, thermal resistance, and intended application. Common types of plastics used in injection molding include:
- Polypropylene (PP): Known for its versatility, it is widely used for containers, automotive parts, and consumer goods.
- Polyethylene (PE): Offers excellent chemical resistance and is commonly used for packaging applications.
- Polyvinyl Chloride (PVC): Frequently used in construction materials, it is durable and resistant to environmental degradation.
- Thermoplastic Elastomers (TPE): Combining the properties of rubber and plastic, TPEs are often used for soft-touch applications.
- Acrylonitrile Butadiene Styrene (ABS): Known for its strength and impact resistance, ABS is popular in consumer electronics and automotive components.
Benefits of Injection Mold Plastics
Injection mold plastics offer numerous advantages that have made them the go-to option for manufacturers across various sectors:
1. High Efficiency and Speed
Injection molding is capable of producing large volumes of parts rapidly. The quick cycle times enable businesses to meet high demand without compromising quality. This efficiency translates into lower labor costs and increased productivity.
2. Design Flexibility
With injection molding, intricate designs and complex geometries can be achieved with relative ease. Injection mold plastics can be customized to match specific requirements, making them suitable for a diverse range of applications.
3. Consistent Quality
One of the most significant advantages is the ability to maintain uniform product quality. The automated nature of the process minimizes human error, ensuring that each part meets the specified tolerances and standards.
4. Material Efficiency
The injection molding process produces minimal waste. Excess plastic can often be recycled and reused, making this method more sustainable compared to traditional manufacturing processes.
5. Cost-effectiveness
Despite the initial costs of mold creation, the long-term savings achieved through high production rates, efficiency, and reduced waste lead to overall cost-effectiveness, especially for large production runs.
Applications of Injection Mold Plastics
Injection mold plastics find their application in numerous fields, showcasing their versatility and reliability:
1. Automotive Industry
The automotive sector heavily relies on injection mold plastics for manufacturing components such as dashboards, door panels, and under-the-hood parts. These plastics help reduce vehicle weight, enhance fuel efficiency, and meet stringent safety regulations.
2. Consumer Electronics
From smartphone casings to home appliances, injection molded parts are pivotal in the electronics industry. The ability to create lightweight, durable, and aesthetically pleasing parts makes injection molding ideal for this sector.
3. Medical Devices
Injection mold plastics are essential in producing medical devices due to their ability to meet hygienic standards. Products like syringes, surgical instruments, and housings for electronic medical devices are often made through this method.
4. Packaging Solutions
In the packaging industry, injection molding is used to create robust containers, caps, and closures that ensure product safety and integrity while providing eye-catching designs.
5. Industrial Applications
Many industrial components, such as fittings, seals, and containers, utilize injection molded plastics due to their durability and resistance to chemicals and environmental factors.
Future Trends in Injection Mold Plastics
As technology continues to advance, the injection molding industry is evolving. Key trends to watch for include:
1. Sustainability Efforts
With growing environmental concerns, emphasis on sustainable materials and processes is intensifying. Companies are exploring biodegradable plastics and recycling methods to minimize the ecological footprint of injection molding.
2. Advanced Manufacturing Technologies
Technological advancements such as 3D printing and automation are being integrated into injection molding processes, allowing for greater flexibility and efficiency in production.
3. Smart Molding Solutions
IoT (Internet of Things) technologies are enhancing the monitoring of the injection molding process. This leads to predictive maintenance, reduced downtime, and improved quality control.
4. Customization and Personalization
Consumers increasingly demand customized products. Injection molding technology is adapting to meet these needs, allowing for intricate, personalized designs in shorter production runs.
Choosing the Right Partner for Injection Mold Plastics
When considering injection mold plastics for your business needs, it is essential to choose a reliable partner. DeepMould.net is a leader in the field, offering:
- Expertise: Extensive knowledge in the industry allows for tailored solutions that meet specific project requirements.
- Quality Assurance: Rigorous testing and quality checks ensure that every product meets high standards.
- State-of-the-Art Technology: Utilizing the latest advancements in manufacturing technologies for optimal results.
- Customer-Centric Approach: Focusing on client satisfaction with flexible solutions and reliable support.
Conclusion
Injection mold plastics are at the forefront of modern manufacturing, offering unparalleled advantages in efficiency, quality, and design flexibility. As industries continue to evolve, the role of these materials will only grow more critical.
By understanding the intricate details and applications of injection mold plastics, businesses can make informed decisions about their manufacturing processes, aligning with market trends and customer demands. Partnering with experts like DeepMould.net will enable you to harness the potential of injection mold plastics, ensuring successful outcomes for your projects.